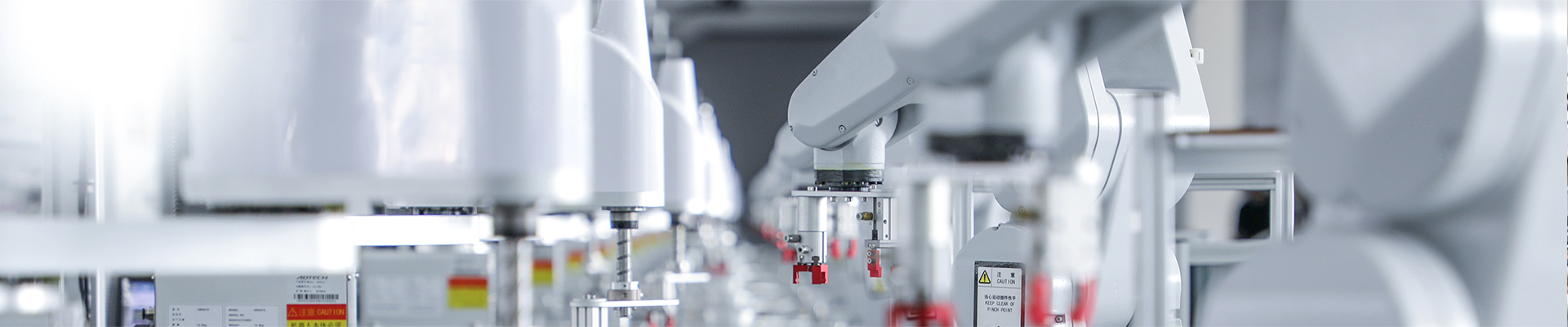
What are the best practices for inspection, maintenance, and storage of "Cable Stringing Tools" to ensure their longevity and safe operation?
2025-07-20Given the critical safety role and high-stress environment of "Cable Stringing Tools," rigorous inspection, maintenance, and proper storage are paramount to ensuring their longevity, preventing failures, and guaranteeing worker safety.
1. Pre-Use & Post-Use Inspection (Operator Level):
-
Visual Damage Check: Before each use, thoroughly inspect all tools for visible damage: cracks, bends, deformation, excessive wear, corrosion, loose fasteners, fraying on ropes or slings, or compromised insulation (for hot sticks or insulated tools). Pay special attention to load-bearing components like jaws on grips, sheave grooves on blocks, and connecting pins.
-
Functionality Check: Operate all moving parts to ensure smooth action without binding, excessive play, or unusual noises. Test safety mechanisms (e.g., locks on clamps, emergency releases on hoists).
-
Cleanliness: Ensure tools are free of dirt, mud, grease, and cable residue. For stringing blocks, check that the sheave rotates freely and the groove is clean.
2. Regular Preventative Maintenance (Qualified Technician Level - Monthly/Quarterly):
-
Cleaning & Lubrication: Thoroughly clean all tools. Apply manufacturer-recommended lubricants to all pivot points, bearings (on swivels and blocks), and moving mechanisms to prevent wear, corrosion, and ensure smooth operation.
-
Wear Part Inspection & Replacement: Regularly inspect components prone to wear, such as the liner materials in stringing blocks (if replaceable), jaws on grips, and cutting edges. Replace worn parts according to manufacturer guidelines before they compromise performance or safety.
-
Rope & Sling Integrity: For fiber ropes or steel wire slings used with tools, inspect for cuts, abrasions, excessive wear, kinks, or damaged splices. Retire damaged ropes immediately.
-
Hardware Checks: Inspect all shackles, clevises, pins, and connection points for deformation, wear, or cracks.
-
Insulated Tools: For hot sticks and other insulated tools, perform dielectric integrity checks as per industry standards and manufacturer recommendations. Any visible damage to insulation should lead to immediate removal from service.
3. Calibration & Certification (Specialized Service Provider - Annually/Bi-Annually):
-
Dynamometers & Load Cells: These critical measuring tools must be professionally calibrated by a certified laboratory at regular intervals (typically annually or bi-annually) to ensure their accuracy. Maintain meticulous calibration records.
-
Crimping Heads/Dies: If hydraulic crimping tools are part of your stringing tools, ensure their heads and dies are inspected for wear and that the hydraulic system provides the correct pressure for consistent crimps.
4. Proper Storage:
-
Clean & Dry Environment: Store all tools in a clean, dry, and well-ventilated area, protected from direct sunlight, extreme temperatures, dust, and moisture to prevent rust and material degradation.
-
Organized Storage: Use dedicated toolboxes, racks, or shadow boards to organize tools. This prevents damage from tools rattling against each other and makes it easy to identify missing or damaged items quickly.
-
Protective Covers/Cases: Store sensitive tools (e.g., dynamometers, precision measuring tools) in their original padded, protective cases to shield them from impacts and environmental factors.
-
Separate Insulated Tools: Store insulated tools separately to prevent damage to their insulation from contact with other tools or sharp objects.
5. Removal from Service:
-
Immediate Tagging: Any tool that shows significant damage, a compromise to its integrity (especially safety-critical components or insulation), or fails a functional check must be immediately tagged "OUT OF SERVICE" and removed from use.
-
Professional Repair/Replacement: Do not attempt to repair safety-critical or specialized tools unless you are a certified technician following strict manufacturer guidelines. Often, replacement is safer and more cost-effective than attempting field repairs.
Adhering to these rigorous practices significantly extends the working life of your valuable "Cable Stringing Tools," maintains their precision and performance, and, most importantly, safeguards the lives of your line workers.